材料的主要失效形式有:磨损、腐蚀、疲劳等,一些调查数据显示:因磨损、腐蚀、疲劳等源于材料表面的失效形式占了80%以上,可见材料表面的结构和性能对材料综合性能有着至关重要的影响。在载荷的作用下,构件的疲劳断裂往往源于材料表面产生的裂纹,裂纹的进一步扩展可能导致材料的整体破坏,甚至导致设备故障。
为提高零部件的可靠性,延长材料的使用寿命,在不改变基体材料性能的前提下,表面强化技术与方法得到了广泛应用,取得了良好的经济效益。
随着航空航天、武器、核能、交通等高端设备的发展,对其零件表面性能要求也越来越高,传统的喷丸、表面滚压等强化技术渐渐难以满足高性能设备的生产要求,而激光冲击强化技术很好地解决了这些问题。与传统的表面强化技术相比,激光冲击强化获得更深残余应力层、产生加工硬化、细化晶粒的优势,能够显著提高材料的疲劳寿命,在各个领域有着广泛应用,获得了越来越多的青睐。
激光冲击强化(LSP)又名激光喷丸,是一种新型表面强化技术,具有显著的技术优势,能够带来与众不同的技术解决方案,在工业界越来越受重视。
激光冲击强化的基本原理如下图所示。

图 激光冲击强化原理图
该技术的基本原理为:短脉冲(几十纳秒)、高峰值功率密度(>109 W/cm2)的激光透过透明约束层(一般采用材料有:流水、有机玻璃等)后作用在工件表面,涂覆在工件表面的吸收涂层(一般采用材料有铝箔、黑胶带、黑漆等)吸收激光能量并发生爆炸性气化,形成等离子团进一步吸收激光能量,产生温度t>107℃、压强P>1 GPa的等离子体;该等离子体在约束层的限制作用下,形成GPa级瞬时高压等离子体冲击波,并向工件材料内部传播;在冲击波的力学效应作用下,由于冲击波峰值应力极高,远超材料的屈服极限,材料表层发生塑性变形,引起晶格畸变、位错、位错交织、位错墙、晶粒细化等微观织构变化,产生了平行于材料表面的拉应力;根据力学效应的反作用原理可知,在等离子体冲击波作用结束后,材料表面将形成一定深度的残余压应力层,从而实现对零件的表面强化或精密成型加工,大幅提高金属材料的耐磨损、抗应力腐蚀和抗疲劳等性能。
激光冲击强化不同于传统表面强化技术,其典型的约束层与吸收保护层原理结构可以显著增加冲击波压力,进而对材料进行强化。这种强化方式具有高压(GPa级)、高能(GW量级)和超高应变率(>106 s-1)的特点。
与传统的激光切割、激光淬火、激光焊接等利用激光热效应的激光加工技术不同,激光冲击强化则是一种利用激光冲击波力学效应的表面改性技术,在加工过程对工件几乎没有热效应。
因激光冲击强化技术具有上述优势,近年来发展迅速,目前主要应用于航空航天与国防军工领域。随着该技术的不断成熟,激光冲击强化技术在船舶制造业、核工业、石油化工行业、生物医疗、轨道交通、电网电力等领域展示出了无可比拟的技术优势,拥有着巨大的应用前景和商业价值。
20世纪60年代,美国科学家发现了激光诱导冲击波现象。与此同时,我国的钱临照先生也发现了此现象,提出冲击波有可能对材料作用后使材料位错密度增加的概念。由于受当时实验条件和应用背景的影响,激光冲击强化技术在20世纪70年代才开始得到实际研究,而受到广泛重视和快速发展则是上世纪末的事情。五十多年来,该技术取得了巨大进步,技术也日益成熟,带动了一大批产业的发展。
1972年,美国巴特尔学院(BMI)的Fairand等人通过短脉冲、高功率密度激光诱导的冲击波来改变7075铝合金的显微结构组织,发现经激光冲击强化试验后,合金的疲劳寿命与抗应力腐蚀能力得到一定幅度的提高。这是激光冲击强化实验研究的首次尝试,其采取的强化方式属于无约束层模式,主要用来验证激光冲击强化技术的可行性。1977年,BMI的Calaur等人通过在样品表面使用不同的约束层和涂层材料组合来改变应力波的大小和持续时间,发现在有约束层的模式下,冲击波压力可以达到GPa级且材料疲劳寿命显著提高。这种由透明约束层与吸收涂层的组合方式也成为了激光冲击强化的典型模式。当时由于缺少性能可靠、短脉冲高功率密度的激光器,激光冲击强化技术未能得到实际应用。1984年,美国劳伦斯∙利弗莫尔国家实验室(LLNL)成功研制出世界上第一台具有板条结构的钕玻璃激光器,促进了激光冲击强化技术的发展。
20世纪90年代,美国推出针对航空航天发动机高周疲劳断裂的“高周疲劳科学与技术”(high cycle fatigue science and technology program)计划,该计划旨在提高材料的高周疲劳设计水平,提高飞机的安全性能,该计划的横空出世将激光冲击强化技术由实验室推向了工业应用。在该计划提出后的几年内,美国成功将激光冲击强化技术用于增强Ti-6-4、Al2024-762、IN718和Al7075-77351等发动机合金材料的疲劳寿命。由于激光冲击强化的效率不高,处理时间较长,无法快速去除喷射涂层。1997年,涂层快速处理系统在美国应运而生,该系统能够快速地在工件上涂覆吸收涂层和去除涂层。且首先应用在军用燃气涡轮发动机叶片的激光冲击强化处理,强化效果相当不错。同年,日本科学家Sano在水浸材料的激光冲击强化实验过程中发现:等离子体在空气中的膨胀速度约为声速的20倍,而在水中的膨胀速度仅与声速相当,这为水作为常用约束层提供了数据依据。
21世纪以来,激光冲击强化技术取得了更为惊人的进步,其应用领域也不断扩大,如:汽车关键零部件、水轮机叶片、大型汽轮机、石油管道、纳米仿生等领域。
2003年,激光冲击强化技术被用于波音飞机的叶片处理,标志着激光冲击强化技术开始应用于军民两用飞机领域。2007年,日本开发了微激光冲击强化(MLSP)技术,成功用于核电站压力容器的强化处理,极大提高了压力容器焊缝的抗腐蚀性能。该技术的成功应用,还促进了水下作业激光器与光纤传输技术的发展。随着激光冲击强化工业化应用水平的不断提高,一系列技术瓶颈有待突破,除设备价格和运行成本因素外,人们希望开发可现场操作的便捷设备,在设备出现故障的时候以最快速度解决问题,节约时间与成本。2012年,美国MIC公司取得重大突破,成功研制出可移动式激光冲击强化设备,如下图所示。该设备的诞生,解决了激光冲击强化现场作业难题。
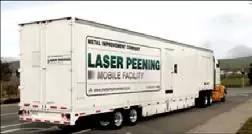
图 可移动式激光冲击强化设备
为了获得更好的激光冲击强化效果,2010年,美国在原有激光冲击强化技术的基础上,结合热力耦合效应在材料表面强化方面的优势,提出温度辅助的激光冲击强化技术,即激光温喷丸(WLP)技术,其工艺原理见下图。由于目前激光温喷丸技术应用的理论和背景相对不多,需要科研工作者不断完善与研究。2017年,美国的Kalentics等用激光冲击强化技术对选择性激光熔化(SLM)部件进行相关实验,提出将SLM和LSP这两个过程结合起来的“3D LSP”方法,将激光冲击强化技术推向一个新高度。
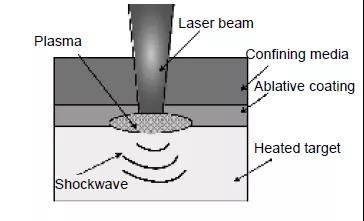
图 激光喷丸原理图